Best Practices For Insulating Your Basement With Spray Foam
Basements traditionally are damp, smelly, mouldy and just down right uncomfortable places to be. In many cases they aren’t even particularly well suited to storage let alone a usable living space. The fact of the matter is that technology and our understanding of building science has come a long way and most basements new and old can be brought up to a standard that will not only save you money in the long run but also make your home safer for your family. In this article we are going to discuss what the best practices are to use when insulating your basement with spray foam insulation.
Why Are Basements Damp and Smelly?
First things first, it’s important to understand why basements are usually damp and smelly to begin with. Some basements do in fact leak and must be dealt with before proceeding, but, in many cases the moisture that forms on the basement walls is actually condensation caused by the temperature differential between the warm air in the house and the cold walls. The warm air comes in contact with the cold walls and condenses into water, similarly to a cold drink on a hot day. The walls don’t get warm enough or sufficient air movement to completely dry. This water formation provides the perfect breeding ground for mould. The smell that is typically associated with a basement is actually caused by that mould.
Traditional Basement Insulation Methods
Okay, let’s talk about the traditional way we have seen basements insulated in the past. A 2×4 wall is framed around the outer perimeter of the basement, sometimes a tar paper type product is put in place first, any electrical and plumbing is roughed in. Next, the stud cavities and rim joist cavities are stuffed with a friction fit product, usually fiberglass batts, sometimes rock wool batts are used. Finally plastic vapour barrier is installed over top of everything according to the Ontario Building Code. This seems like a simple system, so why does it fail to prevent dampness and mould in most cases? Conventional fiberglass and poly air/vapour barriers are very difficult to properly install in basements. They require perfect vapour and air barrier installations and this is just not achieved in 98% of the installations. Once moisture has formed in the wall, the drying out process is extremely slow because of the vapour barrier. Once fiberglass batts have gotten wet they are permanently ruined.
So what we need is an air impermeable system to isolate the warm interior air from the cold exterior walls. This means you need a foam product. You could theoretically use a foam board product, the problem is, in order to create that 100% air barrier we need, you will have to fit the foam board into all the rim joist areas and also air seal the entire job with tape or caulking. This is going to be a lot of work and ultimately will suffer from a lot of the same issues as the fiberglass batts.
Air Sealing
We know why the other systems fail, so let’s take a look at why spray foam insulation really is the best option for any basement. First and foremost is the obvious: Air Sealing! We know that moisture problems are caused by a lack of air sealing, spray foam insulation is as the name implies, sprayed in place. That means we can create one giant perfectly fitted piece of insulation that is sealed on the bottom, top and in all those rim joist cavities. Second, 2lb medium density spray foam insulation has a much higher R-value per inch then other products on the market. 2lb medium density spray foam insulation is also waterproof, this means if you do have a flood in your basement, the insulation will not be damaged.
Simply put, spray foam insulation is the best way to insulate any basement, so why isn’t it used in every house? The Ontario Building Code is starting to mandate more continuous insulation in new homes. The main reason is the upfront cost. What does it cost to insulate a basement with spray foam insulation? The answer is, it’s going to cost about twice as much as the traditional fiberglass/poly route. Of course, this is the up-front cost, you will see significantly reduced heating bills as well as a much more comfortable and safe home for your family. Studies have shown it only takes a handful of years to recoup this initial investment but the benefits of spray foam insulation in your basement will last a lifetime.
Here’s a few common questions we get about basement insulation projects:
Should we build the framed walls before or after the spray foam insulation is installed?
Typically, the framing is done prior to the spray foam being installed. This will allow you to maximize the floor space of the finished product. With that being said, some rim joist cavities can be difficult to access after the walls are built. Some special attention has to be given to those areas. In some cases, it’s better to spray first to ensure we get that good quality seal from bottom to top.
Are there any special framing requirements for spray foam insulation?
The short answer is no. There are no special framing methods needed but there are some optimizations you should do.
- Space the framing out from the actual basement walls at least 1 inch. This allows the foam to go behind all the framing members which creates a continuous seal of insulation to eliminate air leakage and maximize performance.
- Many times the framing can be done with 2×3 lumber because once its locked into the spray foam it will be very strong. This cuts on cost and also increases the amount of usable floor space slightly which can be handy in small basements.
- California corners – this framing technique makes it easier to get good R-value and air seal in the corners.
How much foam do I need?
For many years the standard for spray foam insulation in basements in Ontario has been 2” (R-12.4). In the last couple of years, as the Ontario Building Code Standards change, we have seen 3” (R-19.6) become a common option as well. You will have to decide based on your budget but as a rule of thumb we say, living space needs 3” and storage space can get away with 2”. Let’s face it, 2” of spray foam insulation from top to bottom is going to outperform anything else on the market; 3” is just a bit better yet.
Does spray foam insulation need to be covered?
According to the Ontario Building Code, yes, all foam products, spray foam included, must be covered with a thermal barrier. In most cases ½” drywall will be installed which is considered an acceptable thermal barrier. In cases where drywall won’t be used (unframed basements), we can install DC315 thermal barrier over the finished foam to satisfy the thermal barrier requirements.

What to Expect?
When you work with Ecocomfort Spray Foam, here’s what you can expect from our spray foam insulation installers:
-
Thorough Assessment: We conduct a detailed assessment of your property to understand your insulation needs and recommend the best solutions.
-
Customized Recommendations: Based on our assessment, we provide personalized recommendations for spray foam insulation that align with your budget and objectives.
-
Efficient Installation: Our installers ensure efficient and precise spray foam insulation installation, minimizing disruptions and maximizing insulation benefits.
-
Quality Assurance: We conduct post-installation inspections to ensure that the insulation meets our high quality and performance standards.
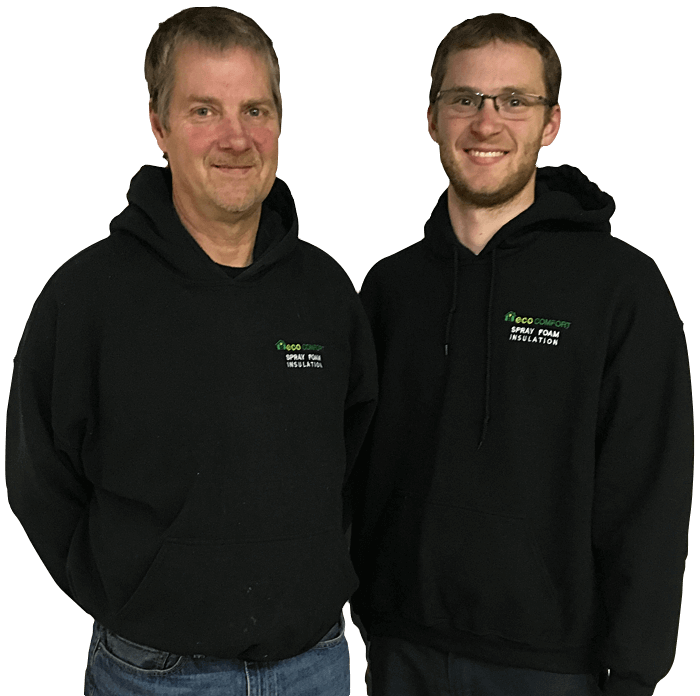